Advanced Manufacturing: Cobalt Chrome in 3D Printing
3D printing, also known as additive manufacturing, has significantly transformed various industries by allowing complex designs to be created with precision and efficiency. Among the various materials used in 3D printing, cobalt chrome (CoCr) stands out due to its exceptional properties and diverse applications. In this post, we delve into the world of 3D printing with cobalt chrome, exploring its benefits and applications.
What is Cobalt Chrome?
Cobalt chrome is an alloy composed primarily of cobalt and chromium, often with added elements like molybdenum and tungsten. Known for its high strength, excellent wear resistance, and biocompatibility, cobalt chrome is extensively used in industries that require durable and reliable materials.
Advantages of 3D Printing with Cobalt Chrome
1. Excellent Mechanical Properties
Cobalt chrome's high strength and resistance to corrosion and wear make it ideal for parts that need to endure harsh conditions. This makes it a preferred material for aerospace, automotive, and medical applications.
2. Precision and Complexity
3D printing allows for the creation of intricate designs that are challenging or impossible to achieve with traditional manufacturing methods. This capability is particularly beneficial for producing complex geometries in medical implants and aerospace components.
3. Biocompatability
Cobalt chrome's biocompatibility ensures that it can be safely used in medical applications, such as dental implants and orthopedic devices. The alloy's compatibility with the human body reduces the risk of adverse reactions, making it an excellent choice for permanent implants.
4. Patient Specific Customisation
The flexibility of 3D printing enables the production of customised parts tailored to specific requirements. In healthcare, this means patient-specific implants and prosthetics can be created, enhancing the effectiveness and comfort of medical treatments.
Applications of 3D Printing with Cobalt Chrome
Medical and Dental Implants
Cobalt chrome is widely used for making dental crowns, bridges, and orthopedic implants.
Aerospace Components
3D printed turbine blades, engine components, and other critical parts made from cobalt chrome enhance the performance and longevity of aerospace machinery.
Automotive and Motorsport Parts
In the automotive sector, cobalt chrome is used to produce high-performance parts that require durability and precision. Engine components, transmission parts, and other elements benefit from the material's properties, contributing to more efficient and reliable vehicles.
Why use LAS for 3D Printing Cobalt Chrome?
Printing with cobalt chrome is notoriously tricky due to its complex melting and solidification properties. Our team at LAS possesses the specialised knowledge and expertise necessary to navigate these challenges, ensuring the production of high-quality parts.
LAS offers 3D printed Cobalt Chrome parts from two different technologies. Theses are Laser Powder Bed Fusion and Laser Directed Energy Deposition (Laser Metal Deposition). LAS has over 20+ years of Metal Additive Manufacturing experience.
Interested in 3D Printing Cobalt Chrome? Send an Enquiry now.
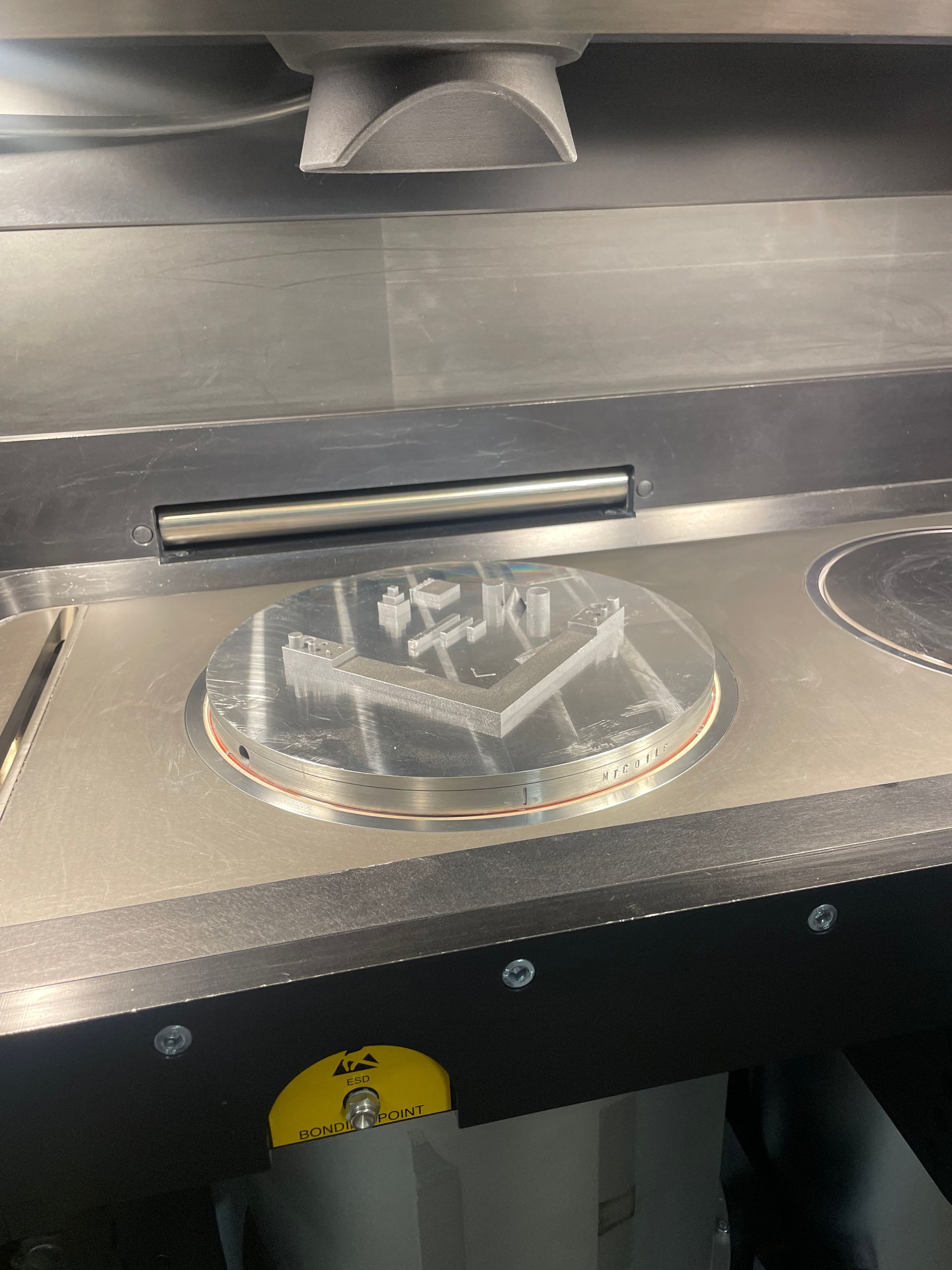
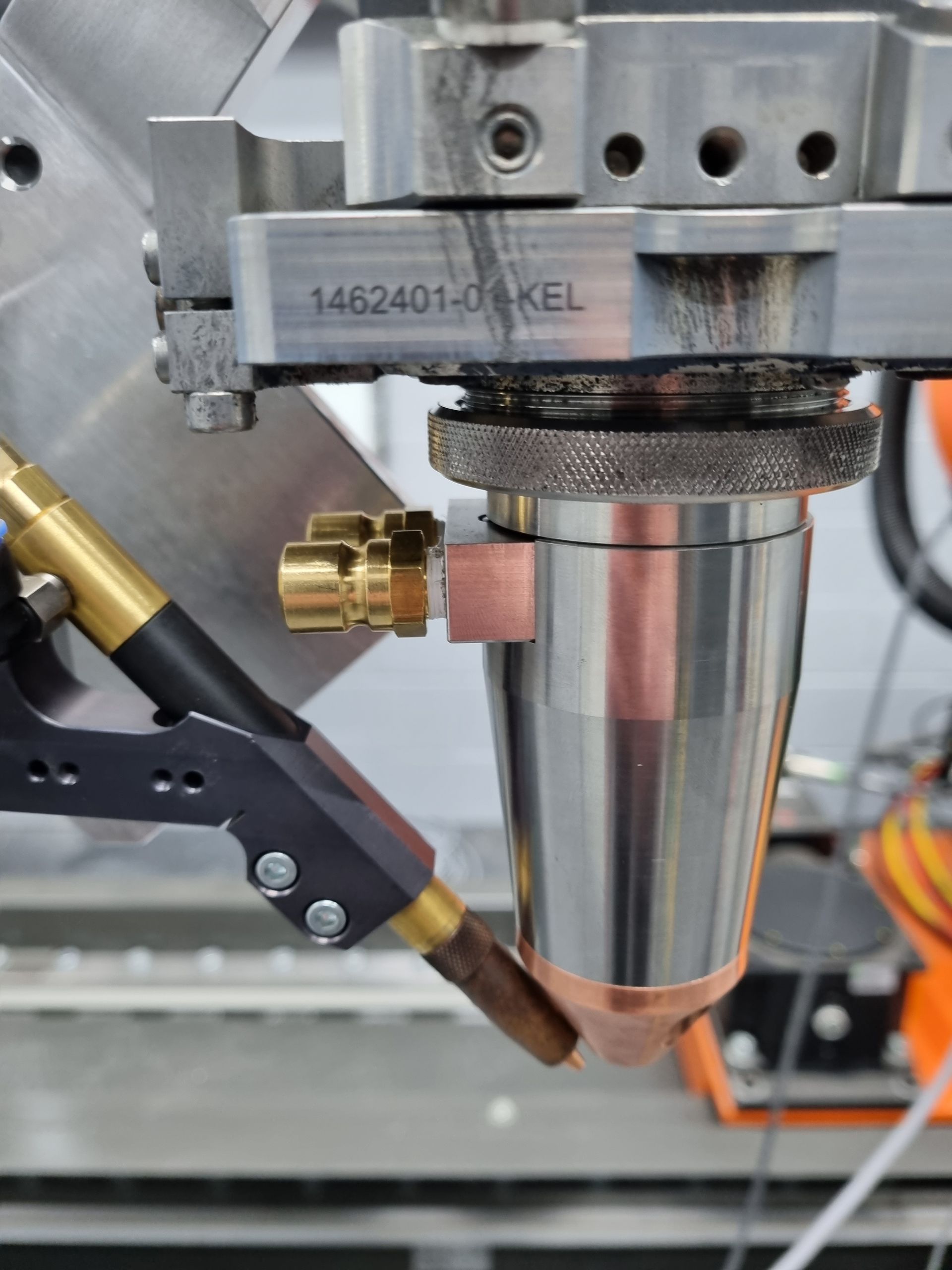